Penetrant inspection is a brilliant method for finding surface defects usually for non-ferrous materials.
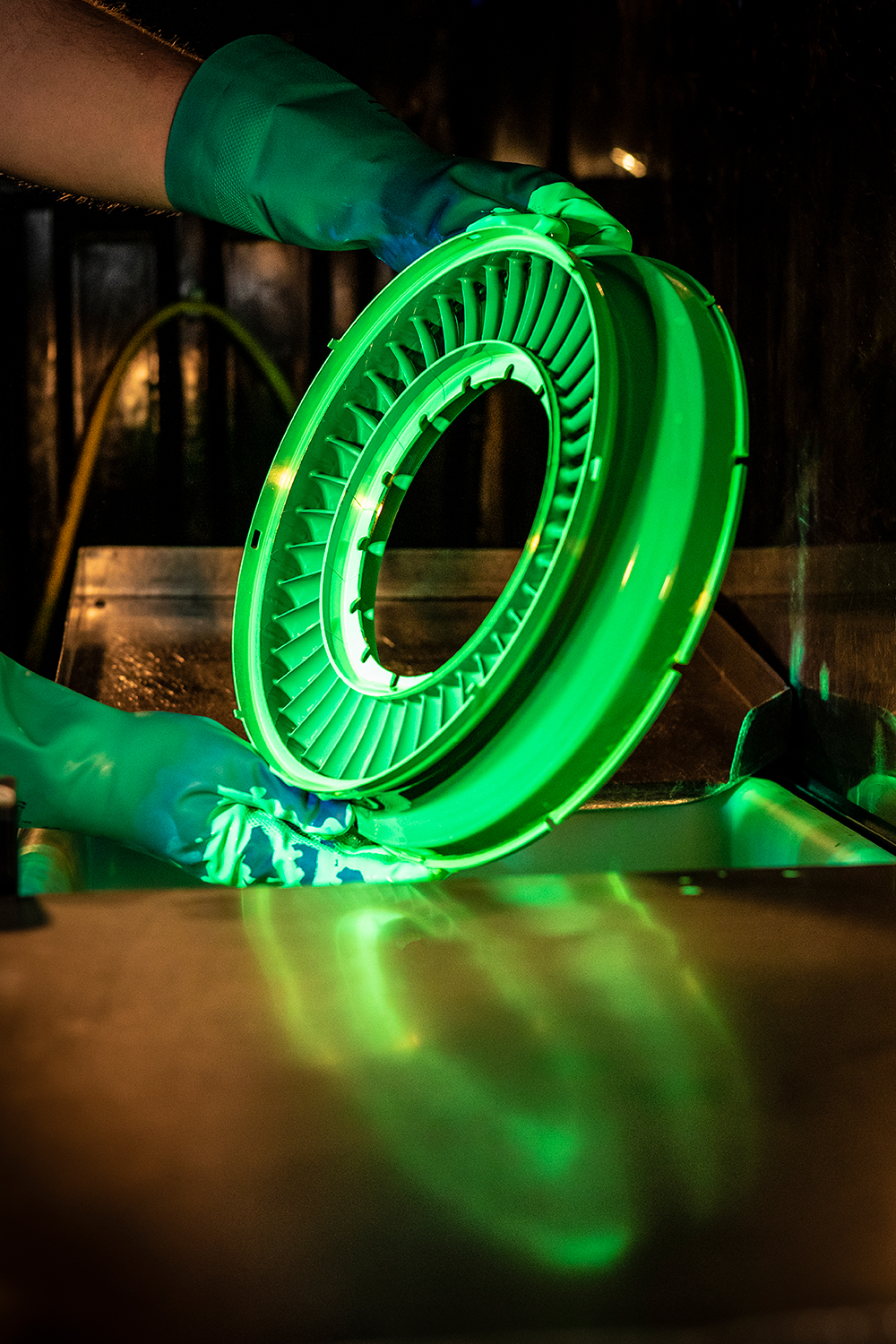
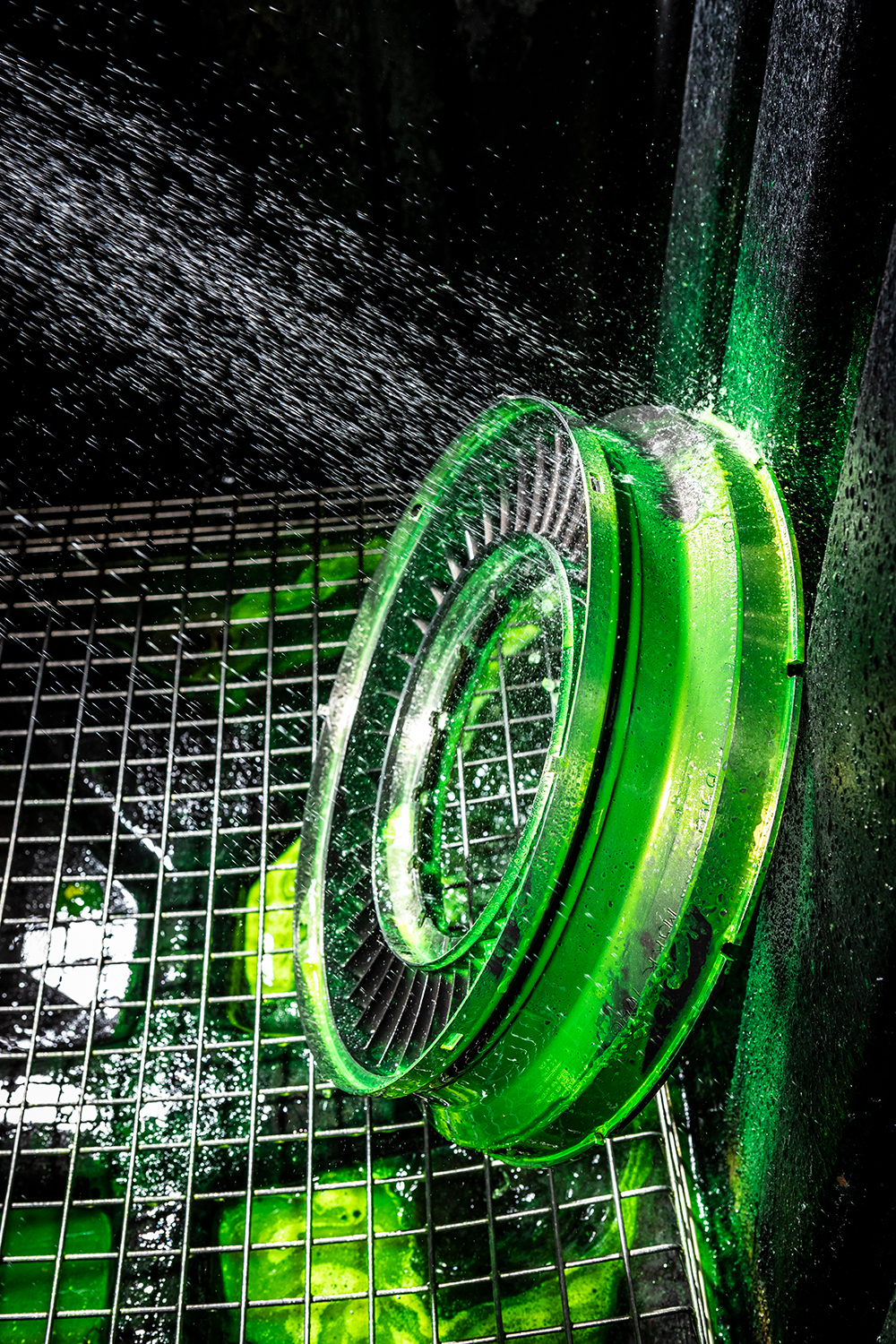
We have extensive knowledge in testing all different types of components using the penetrant inspection method and use of our own specialist equipment is key!
Sub-contract your ASTM E 1417, BS M39, BS EN ISO 3452 (EN 571-1) or other customer specific Penetrant NDT to our accredited test house.
We operate water washable, solvent removal, and post removable systems using a wide range of sensitivity levels. The combination of a wide range of available techniques and decades of experience allow us to operate a first class service – whatever the application.
You can view our approvals on our Quality page.
How does it work?
The penetrant process involves a number of stages with variations of the exact method depending on the form of the product and the defects sought.
The process starts with cleaning and application of a dye. The dye makes its way in to any potential defect open to the surface. The dye is applied liberally to the part surface for good coverage so the next step is to remove the ‘bulk’ dye from the component. This can be carried out by washing with water or cleaning with solvent.
If water is used for the wash process then the part may need to be dried prior to development. For this process a hot air oven is usually used.
Development is the process of drawing out the dye from any discontinuity present and fixing it in place. This can be accomplished in lots of different ways but most commonly a dry chalky powder is used.
Inspection is the final key stage. The operator manually inspects the part for ‘indications’ caused by bleed out of the dye. For fluorescent techniques the dye glows bright green under UV light so inspection in the dark with a UV lamp creates a natural contrast. This gives the inspector the best chance to find the indications and identify any defects.