Magnetic Particle Inspection (MPI) is a complex technique requiring a fundamental understanding to ensure it works efficiently.
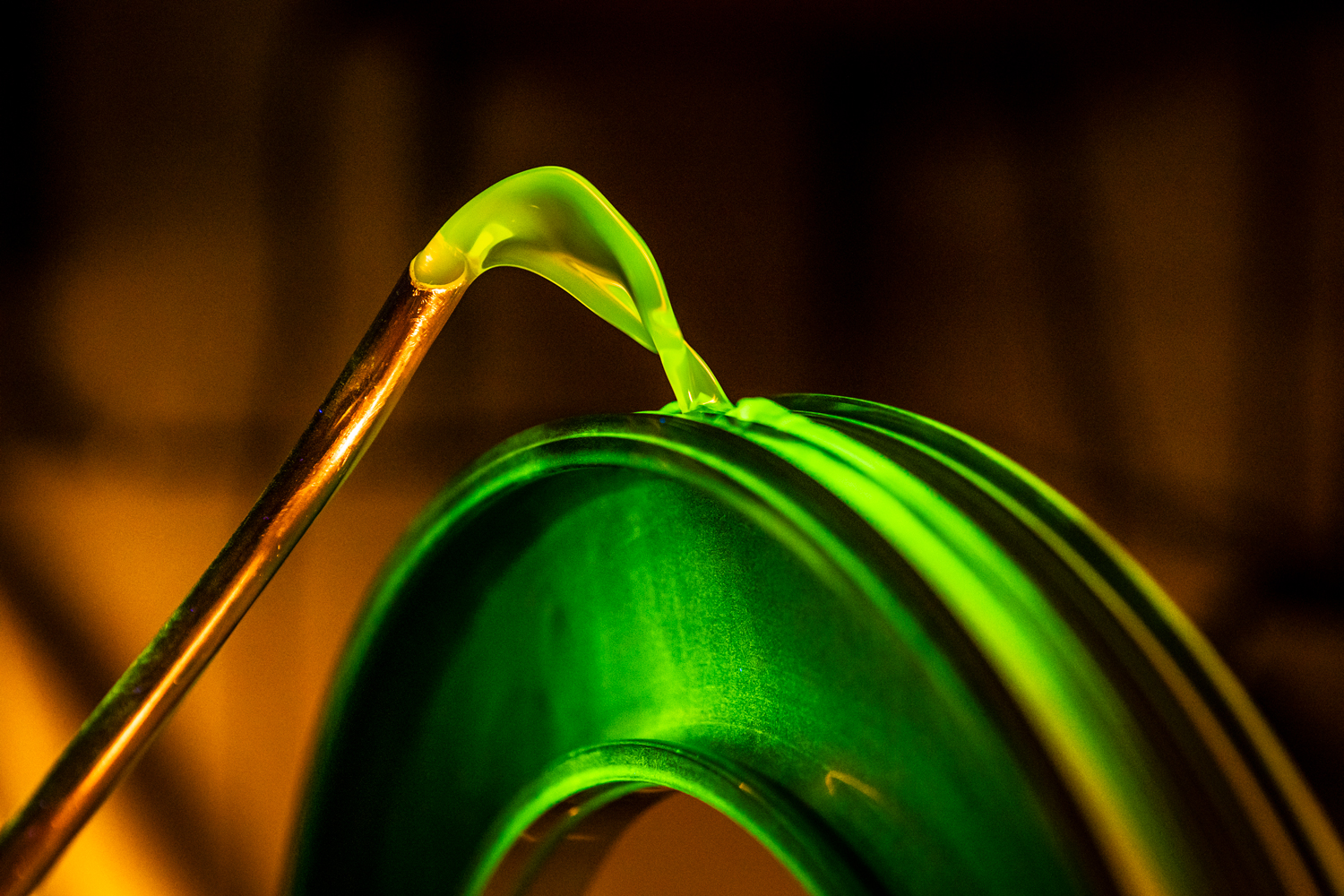
We are MPI specialists. With bespoke equipment and unique capability we can test a wide variety of different components quickly and efficiently where others just can’t.
Whether it’s a critical turbine disc for an aero engine or the crankshaft from a vintage car, magnetic particle inspection offers an effective test method for detection of surface defects in ferromagnetic materials.
You may have a basic requirement to meet ASTM E 1444, BS EN ISO 9934, BS 6072 or some other standard, or simply need an effective test for cracks – In any case our accredited test house holds numerous customer approvals and is ready to meet your needs.
Unique Capability for MPI of complex components
Magnetic Particle Inspection of large or complex parts can be a struggle. You could be struggling to find a test house with capability or be having problems testing parts efficiently on your own equipment.
We have developed sophisticated, efficient techniques within the method, delivering cost savings and excellent test coverage. A bad technique costs time, money and may not be capable of finding the required defects.
You can view our approvals on our Quality page.
How does it work?
Fundamentally MPI relies on Maxwells laws of electromagnetism.
Any electrical current generates a magnetic field. Magnetic fields are capable of exerting a force on ferromagnetic materials. This is shown by the classic experiment of a bar magnet and iron filings. In MPI we use an electrical current to generate a magnetic field inside the component under test.
This magnetic field inside the component follows a certain pattern. The presence of discontinuities (cracks, inclusions etc.) alters this pattern and can cause the magnetic field to unexpectedly exit the component.
Whilst we are applying the current we also apply fine magnetic particles to the surface of the component in an oil based carrier fluid. As the fluid flows over the component the particles are carried along too and gather around where the magnetic field exits the part. The particles themselves are covered in a fluorescent coating. Inspecting in the dark under UV light gives the inspector good contrast and the best chance of seeing the bright indications the process generates to identify defects.
This process is capable of identifying surface breaking and slightly sub-surface defects.